November 9, 2023
The Sirio, a perfect solution, from Meccanotecnica
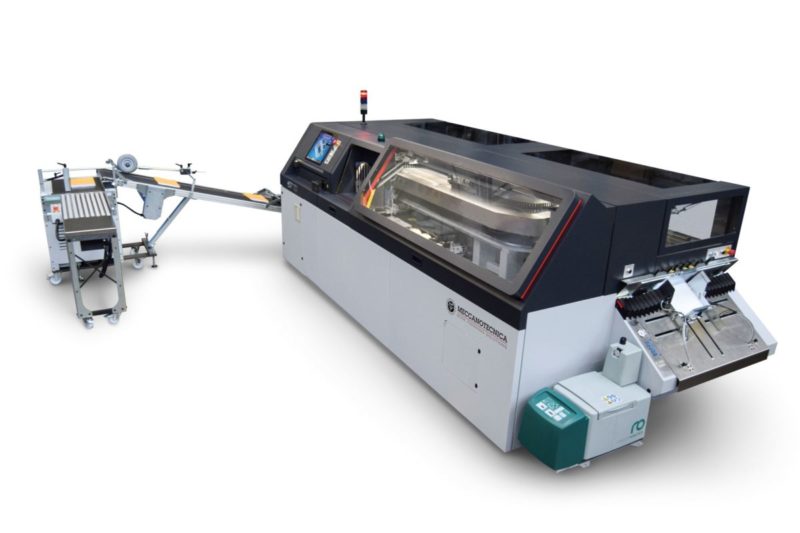
The Meccanotecnica Digital Book Trimming machine has won praise for its speed of trimming variable size books with high quality and multiple functionalities. These include double cutting for oversize trims, and processing books with eight-page gatefold covers in one pass.
Now to complete the system the groundbreaking Sirio digital perfect binder has been launched. It is a completely new development of a three clamp binder, with the capability to run at 1350 copies per hour, and to process single book production.
The digital functionality and control is impressive, but equally important is the industrial build quality of the machine and the rugged design of key elements including 250mm diameter milling head and twin cover scoring shafts. The highest book quality is guaranteed, with a maximum of six scores per cover.
The Sirio has a patented clamp drive system to enable each clamp to be independent, but sharing the drive of one robust chain, ensuring component longevity, and eliminating timing settings. Available now for softcover production, the range will further expand during next year with the introduction of automatic book feeding, book endpapering, PUR spine gluing, and a lining station for hard-cover book production.
The Sirio adhesive binder reflects a shift in emphasis for Meccanotecnica. Building on their long-time expertise in sewn book machine design and production they are utilising their extensive R&D facility to become a leading full solution provider in book finishing.